What is Porosity in Welding: Ideal Practices for Avoiding Permeable Welds
What is Porosity in Welding: Ideal Practices for Avoiding Permeable Welds
Blog Article
Porosity in Welding: Identifying Common Issues and Implementing Ideal Practices for Avoidance
Porosity in welding is a pervasive issue that typically goes unnoticed up until it triggers considerable issues with the stability of welds. This typical flaw can jeopardize the stamina and toughness of bonded frameworks, positioning safety and security risks and leading to costly rework. By understanding the origin creates of porosity and applying reliable avoidance methods, welders can substantially enhance the high quality and reliability of their welds. In this discussion, we will check out the vital factors contributing to porosity formation, examine its harmful effects on weld efficiency, and go over the finest practices that can be adopted to minimize porosity event in welding procedures.
Usual Reasons of Porosity
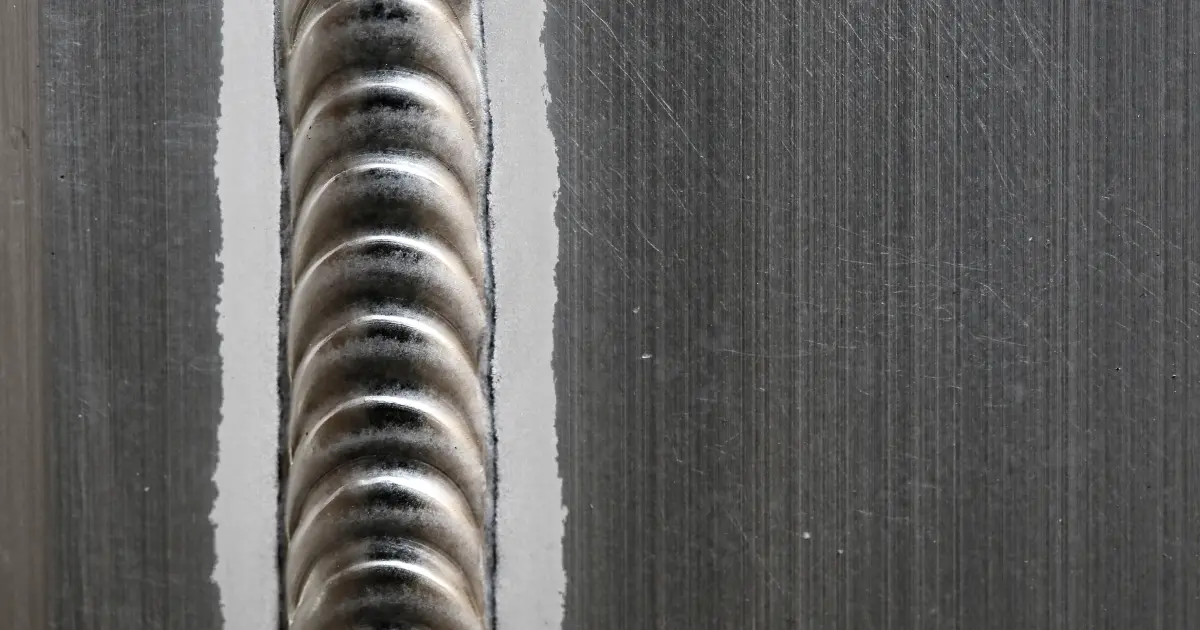
Utilizing dirty or damp filler materials can present contaminations right into the weld, contributing to porosity issues. To alleviate these usual reasons of porosity, comprehensive cleansing of base steels, proper shielding gas option, and adherence to ideal welding specifications are important techniques in achieving high-quality, porosity-free welds.
Influence of Porosity on Weld High Quality

The visibility of porosity in welding can significantly endanger the structural honesty and mechanical properties of welded joints. Porosity produces spaces within the weld metal, weakening its general toughness and load-bearing ability. These gaps work as tension concentration points, making the weld extra at risk to fracturing and failing under used tons. Furthermore, porosity can decrease the weld's resistance to rust and other environmental factors, better decreasing its long life and efficiency.
One of the primary effects of porosity is a decrease in the weld's ductility and durability. Welds with high porosity levels have a tendency to display lower impact toughness and decreased ability to flaw plastically before fracturing. This can be particularly worrying in applications where the welded components go through dynamic or cyclic loading problems. Porosity can hinder the weld's capability to efficiently transfer forces, leading to premature weld failure and prospective security risks in essential structures. What is Porosity.
Ideal Practices for Porosity Avoidance
To enhance the structural integrity and top quality of bonded joints, what certain steps can be executed to reduce the occurrence of porosity during the welding procedure? Making use of the right welding technique for the details product being welded, such as adjusting the welding angle and gun placement, can additionally stop porosity. Routine inspection of welds and prompt removal of any type of issues recognized throughout the welding process are important methods to avoid porosity and produce high-grade welds.
Relevance of Appropriate Welding Techniques
Carrying out appropriate welding methods is vital in guaranteeing the structural stability and quality of welded joints, building upon the structure of reliable porosity prevention procedures. Too much heat can lead to boosted porosity due to the entrapment of gases in the weld swimming pool. Furthermore, utilizing the suitable welding parameters, such as voltage, current, and take a trip rate, is vital for attaining sound welds with very little porosity.
Moreover, the selection of welding process, whether it be MIG, TIG, or stick welding, ought to line up with the details requirements of the project to ensure ideal results. Proper cleansing and preparation of the base metal, in addition to choosing the appropriate filler product, are also essential components of efficient welding methods. By sticking to these finest techniques, welders can decrease the threat of porosity formation and produce top quality, structurally sound welds.
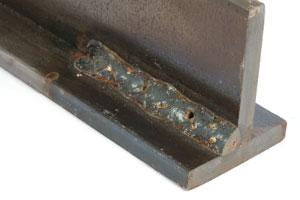
Evaluating and Quality Control Actions
Examining procedures are necessary to discover and prevent porosity in welding, making certain the strength and sturdiness of the last product. Non-destructive screening approaches such as ultrasonic testing, radiographic have a peek here testing, and visual inspection are commonly used to determine potential issues like porosity.
Post-weld assessments, on the various other hand, evaluate the last weld for any kind of defects, including porosity, and validate that it meets specified requirements. Applying an extensive quality control plan that consists of thorough testing treatments and examinations is paramount to decreasing porosity problems and making certain the overall quality of welded joints.
Final Thought
Finally, porosity in welding can be an usual issue that influences the top quality of welds. By recognizing the common reasons for porosity and executing ideal practices for avoidance, such as appropriate welding this article strategies and screening procedures, welders can ensure excellent quality and dependable welds. It is vital to prioritize avoidance techniques to reduce the occurrence of porosity and find here preserve the honesty of bonded structures.
Report this page